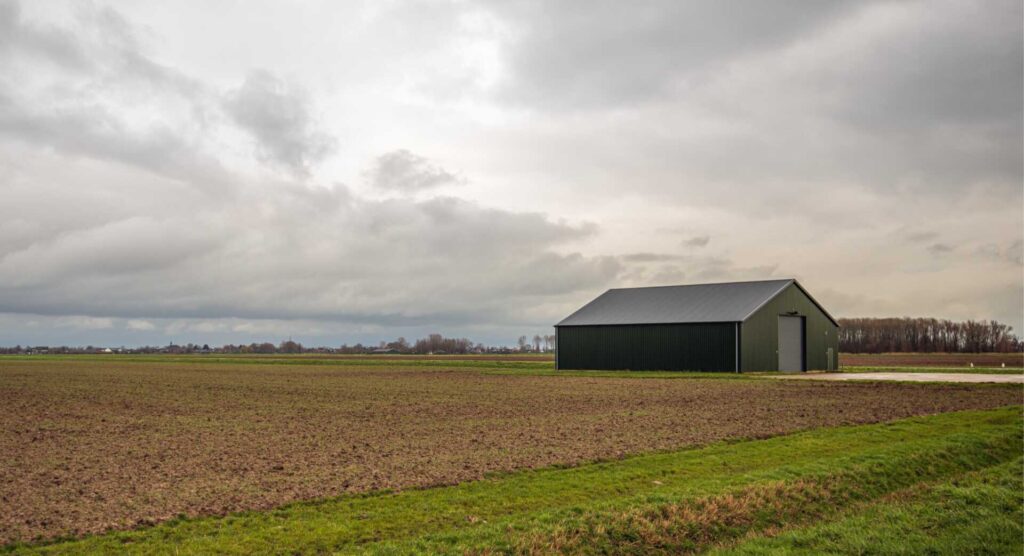
Contents
Understanding how to effectively budget for your metal building project is important for its success. From initial cost assessments to long-term maintenance considerations, there are various tips and strategies that can help you navigate the complexities of budgeting for metal building costs. By implementing these budgeting tips, you can make sure that your project stays within budget and achieves your desired outcomes without unnecessary financial strain.
Key Takeaways
- Research metal material prices for cost-effective options.
- Obtain multiple quotes from suppliers for price comparison.
- Factor in labor, installation, and unexpected expenses.
- Choose durable, weather-resistant materials for longevity.
- Opt for energy-efficient options to reduce long-term costs.
Initial Cost Assessment
When evaluating the initial cost of a metal building project, it’s important to conduct a thorough assessment to accurately determine the required budget. Cost estimation forms the backbone of financial planning and budget management in any construction endeavor.
To begin with, defining the project scope is vital. This includes outlining the size of the building, the intended use, any special requirements, and the overall goals of the construction.
A detailed breakdown of the expenses involved in the project is essential for an accurate cost estimation. Consider aspects such as materials, labor, permits, equipment rentals, and any additional services required for the construction. By meticulously analyzing each of these components, you can create a detailed budget that covers all necessary expenses.
Furthermore, it’s critical to anticipate any potential unforeseen costs that may arise during the project. Contingency planning is a fundamental aspect of budget management. Setting aside a portion of the budget for unexpected expenses can prevent financial strain and delays in the construction process.
Material Selection Impact
When considering the impact of material selection on metal building costs, it’s important to analyze the variations in material prices and identify cost-effective options.
Different materials come with different price tags, which can greatly influence your overall budget.
Understanding the cost implications of various material choices will help you make informed decisions when planning your metal building project.
Material Price Variations
How do material price variations impact the overall costs of a metal building project? Material prices can fluctuate due to market trends, affecting the budget of your construction project. To manage these variations effectively, building strong supplier relationships and employing smart negotiation strategies are crucial components to take into account.
Key Impact | Description | Mitigation |
---|---|---|
Price Fluctuations | Material costs can vary based on market trends, impacting project budgets. | Stay informed on market trends to anticipate fluctuations and adjust budgets accordingly. |
Supplier Relationships | Strong relationships with suppliers can lead to better pricing and access to discounts. | Cultivate long-term partnerships with reliable suppliers for cost-effective material sourcing. |
Negotiation Strategies | Effective negotiation can result in lower material costs and favorable terms. | Develop negotiation skills and strategies to secure competitive pricing and favorable terms with suppliers. |
Cost-Effective Options
Selecting cost-effective materials is essential for minimizing expenses and optimizing the budget of your metal building project. When considering material options, look for customization opportunities that can add value without breaking the bank. Opting for eco-friendly solutions benefits the environment and can also lead to long-term cost savings through energy efficiency and reduced maintenance needs.
Exploring alternative financing methods can help spread out the financial burden of your metal building project. Look into financing options that offer favorable terms and low interest rates to make the project more affordable in the long run.
Additionally, consider DIY options for certain aspects of the construction process. Taking on tasks like interior finishing or landscaping yourself can help cut down on labor costs and provide a sense of accomplishment.
Labor and Installation Factors
When calculating metal building costs, it’s important to evaluate the expertise and efficiency of the labor and installation team. Labor efficiency plays a significant role in determining the overall expenses of your metal building project. A skilled and experienced team can work more effectively, potentially lowering labor costs. Additionally, the installation timeline is vital in budgeting for metal building costs. A quicker installation process can reduce labor expenses and allow you to start using your metal building sooner, potentially saving money in the long run.
When assessing labor and installation factors, it’s crucial to analyze various aspects that can impact the overall cost. Below is a table highlighting key elements to take into account:
Labor and Installation Factors | Description |
---|---|
Skill Level of Labor | Highly trained workers may be more efficient, potentially reducing labor costs. |
Installation Complexity | Elaborate designs or features may require more time and labor, increasing overall expenses. |
Project Management | Effective project management can streamline the installation process, saving time and money. |
Equipment Utilization | Proper equipment usage can improve efficiency and reduce labor hours, impacting costs. |
Foundation Considerations
Consider the impact of soil type on your foundation requirements, as different soils may necessitate specific foundation designs.
The cost of excavation can vary greatly depending on the soil conditions and depth required for the foundation.
Explore different foundation material options, such as concrete slab, pier and beam, or insulated concrete forms, to find the most suitable and cost-effective choice for your metal building project.
Soil Type Impact
When assessing the influence of soil type on metal building expenses, prioritize conducting a thorough analysis of the foundation considerations to secure excellent construction outcomes. Site preparation is pivotal to addressing soil variations efficiently.
Various soil types, like clay, sand, or loam, can impact the foundation’s stability, necessitating specific adjustments in the construction process. Additionally, drainage considerations play a critical role in preventing water accumulation around the foundation, which can compromise its integrity over time. Understanding these aspects early in the project can help mitigate potential issues that may arise during construction.
Furthermore, soil type affects the construction timeline and poses scheduling challenges. Certain soil conditions may require additional time for site preparation or foundation work, potentially causing delays in the overall project schedule. It’s crucial to account for these factors when planning the construction timeline to ensure that sufficient time is allocated for managing soil-related complexities.
Cost of Excavation
Excavation costs for metal building foundations can have a significant impact on the overall budget, requiring careful planning and assessment to ensure cost-effectiveness in construction projects. When considering excavation for your metal building, two critical factors to keep in mind are the excavation depth and equipment rental.
Excavation Depth | Equipment Rental |
---|---|
The depth of excavation is determined by the type of foundation required for your metal building. | Renting specialized excavation equipment like backhoes or mini excavators can help streamline the digging process. |
A deeper excavation may be necessary for foundations in areas with unstable soil or high wind loads. | Equipment rental costs should be included in the overall budget to avoid unexpected expenses. |
Consulting with a structural engineer can help determine the appropriate excavation depth for your specific project. | Properly maintained equipment can also enhance efficiency and reduce overall project timelines. |
Foundation Material Options
Exploring different material options for your foundation is important in guaranteeing the structural integrity and longevity of your metal building. When considering foundation materials, two main options are commonly used: concrete slab and pier foundation.
A concrete slab foundation involves pouring a thick layer of concrete directly onto the ground, providing a stable base for your metal building. This option is cost-effective and simple to construct, making it a popular choice for many building projects. However, it’s vital to secure proper site preparation and reinforcement to prevent cracking over time.
On the other hand, a pier foundation consists of concrete piers strategically placed to support the weight of the metal building. This type of foundation is ideal for uneven terrains or areas with expansive soil conditions. While pier foundations may require more labor and materials initially, they offer excellent stability and durability in the long run.
Consider the specific requirements of your site and the intended use of your metal building when selecting the most appropriate foundation material to maintain a solid and reliable structure.
Design Complexity Influence
Consider carefully how the complexity of your design impacts the overall cost of your metal building project. The architectural aesthetics and structural design you choose play a significant role in determining the final expenses. Here’s how design complexity influences costs:
Architectural Aesthetics: Elaborate architectural designs, such as curved roofs or unique facades, can elevate the overall appeal of your metal building but often come with higher price tags due to the specialized manufacturing required.
Structural Design: Opting for intricate structural elements like large spans or unconventional shapes may increase engineering costs and material expenses, impacting your budget significantly.
Customization Possibilities: While customizing your metal building allows you to tailor it to your specific needs and preferences, intricate customization can drive up costs as it requires more labor and materials.
Interior Layout: Incorporating a complex interior layout with multiple rooms, mezzanines, or unique features can add to the overall cost of the project, as it involves additional planning and construction work.
Material Selection: Choosing high-end or specialized materials for a complex design can escalate costs, so balancing aesthetics with budget considerations is essential for a successful project.
Permits and Regulations Impact
When assessing the overall expenses of your metal building project, it’s crucial to take into account how permits and regulations can greatly influence your budget. The permit procedure, legal necessities, zoning limitations, adherence issues, and regulatory obstacles are all vital aspects that can impact the financial components of your project.
Initially, the permit procedure is a crucial stage in ensuring that your metal building project complies with all the necessary legal requirements. Acquiring permits involves submitting detailed blueprints, paying fees, and undergoing inspections, all of which can contribute to the total expenses. Failure to adhere to permit regulations can result in expensive penalties and delays in the construction process.
Furthermore, navigating zoning restrictions is another significant factor to take into consideration. Zoning regulations determine how the land can be utilized, including the type of structures that can be constructed. Failing to follow these regulations can lead to legal complications and additional costs to rectify the project.
Moreover, ensuring compliance with building codes and regulations is vital to avoid potential setbacks. Regulatory obstacles such as environmental impact assessments or historical preservation requirements can also impact the budget of your metal building project. Hence, it’s essential to thoroughly research and comprehend all the legal and regulatory aspects before commencing your construction journey.
Insulation and Energy Efficiency
Understanding the importance of proper insulation and energy efficiency is crucial when planning your metal building project. Investing in high-quality insulation and energy-efficient solutions contributes to a comfortable indoor environment and leads to long-term cost savings.
Here are some key points to keep in mind:
Energy Savings: Opting for quality insulation options can significantly decrease your energy consumption, resulting in lower utility bills and a more environmentally friendly building.
Insulation Options: Explore various insulation materials like fiberglass, spray foam, or rigid foam boards to discover the best fit for your specific requirements and budget.
Environmental Impact: Choosing energy-efficient insulation benefits your wallet and lessens your carbon footprint, aiding in creating a more eco-conscious building.
Long-Term Benefits: Although the initial investment in premium insulation may be higher, the enduring energy savings and durability of your metal building make it a cost-efficient decision in the long run.
Comfort and Productivity: Proper insulation controls temperature and reduces noise levels, establishing a cozy and efficient space for occupants.
Maintenance and Longevity
Proper maintenance of your metal building is essential for maintaining its longevity and structural integrity. Creating a maintenance schedule can help you stay on top of necessary tasks and reap the durability benefits of your metal building. Regular inspections, cleaning, and addressing any issues promptly can greatly extend the lifespan of your structure. Additionally, investing in corrosion prevention measures like protective coatings can further safeguard your building against rust and decay, making it a wise long-term investment.
Maintenance Task | Frequency |
---|---|
Inspect roof for damage | Semi-annually |
Clean gutters and downspouts | Annually |
Check seals on windows and doors | Quarterly |
Touch up paint as needed | As necessary |
Following a maintenance schedule enhances the longevity of your metal building and ensures that it remains in top condition for years to come. By taking proactive steps to prevent corrosion and following a regular maintenance routine, you are safeguarding your investment and securing the structural integrity of your metal building for the future.
Contingency Planning
Take into account potential risks and uncertainties by formulating a detailed backup plan for your metal building project. When it comes to budgeting for metal building costs, having a sturdy backup plan is essential for effective risk management and ensuring the project’s success.
Here are some key aspects to keep in mind:
Risk Management: Identify potential risks that could impact your project, such as material price fluctuations, weather delays, or design changes. Develop strategies to mitigate these risks and minimize their impact on your budget.
Emergency Funds: Set aside a portion of your budget specifically for unforeseen circumstances. Having emergency funds allocated can provide a financial buffer in case unexpected expenses arise during the construction process.
Unexpected Expenses: Anticipate additional costs that may not be initially accounted for in your budget. Factors like permit delays, structural modifications, or site preparation issues can lead to unforeseen expenses that need to be covered.
Financial Buffer: Allocate a backup amount within your overall budget to account for fluctuations in prices or unexpected changes. This cushion can help absorb any financial shocks and keep your project on track without compromising quality.
Adaptability: Stay flexible and be prepared to adjust your budget and timeline as needed. Being adaptable and having a well-thought-out backup plan can help you navigate any challenges that may arise during the construction of your metal building.
Wummary
When budgeting for metal building costs, remember to carefully assess all initial expenses.
Consider the impact of material selection, labor factors, foundation requirements, and design complexity.
Be mindful of permits and regulations, prioritize insulation and energy efficiency, and plan for long-term maintenance needs.
Don’t forget to include contingencies in your budget to avoid any unexpected costs.
Remember, a well-planned budget is the foundation for a successful metal building project.
Recent Posts
What Are the Benefits of Tailored Metal Structures?
Imagine a well-crafted suit tailored to fit perfectly; that’s how tailored metal structures operate in
3 Tips for Long-lasting Metal Commercial Structures
When it comes to metal commercial structures, you’ll want to focus on a few key
Explore Benefits of Residential Metal Structures
It’s funny how you might stumble upon the idea of residential metal structures just when