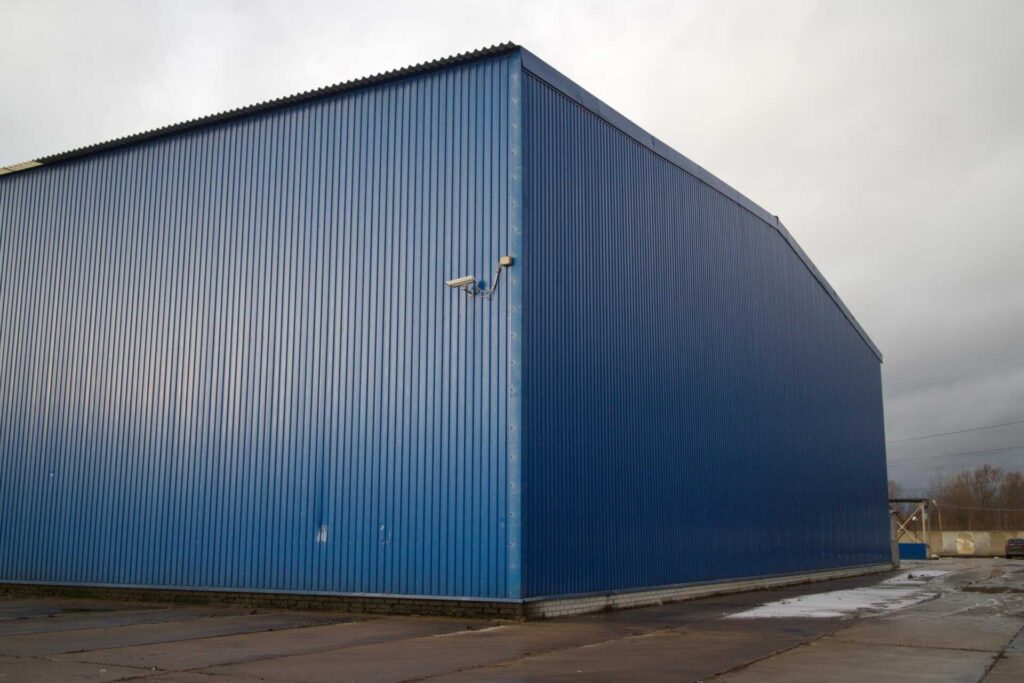
Contents
Imagine estimating metal building costs as journeying through a dense forest with only a dim flashlight. Each step requires precision and foresight to avoid stumbling over hidden obstacles. In this discussion, you will uncover the top five tips that will illuminate your path toward accurate cost estimation. From budget allocation to labor cost analysis, these strategies are the key to opening the door to a successful metal building project.
Key Takeaways
- Obtain multiple quotes for accurate cost estimation.
- Factor in labor costs and negotiate competitive prices.
- Consider material quality and durability for long-term savings.
- Allocate a contingency budget for unexpected expenses.
- Research permit requirements to avoid additional costs.
Budget Allocation
When estimating metal building costs, start by carefully allocating your budget to different aspects of the project to ensure a thorough financial plan. A detailed cost breakdown is essential to make sure you have a clear understanding of where your money is going.
Begin by breaking down the costs into categories such as materials, labor, permits, and any additional expenses that may arise during the construction process. This breakdown will help you identify areas where you can potentially save money through price negotiation with contractors or suppliers.
Price negotiation plays a pivotal role in managing your metal building project expenses. Don’t hesitate to discuss pricing with contractors and suppliers to see if there’s room for adjustments. Remember, being assertive yet respectful can often lead to favorable outcomes.
Consider obtaining multiple quotes to compare prices and make informed decisions. Additionally, be open to exploring different options or materials that could be more cost-effective without compromising quality.
Material Selection
Careful thought of material choices is crucial in optimizing the functionality and cost-effectiveness of your metal building project. Regarding insulation options, selecting the right material can significantly influence the energy efficiency and comfort level of your metal building. Options such as fiberglass, foam board, or spray foam insulation each have their advantages, so evaluating your specific needs and climate conditions is vital for making an informed decision.
Roofing materials play a significant role in protecting your structure from the elements. Factors like durability, maintenance requirements, and aesthetics should guide your choice between options like metal panels, shingles, or tiles. Structural considerations, such as the type of frame and supports used, are crucial in ensuring the safety and longevity of your metal building. Be sure to consult with professionals to determine the most suitable structural design for your project.
Lastly, don’t overlook the impact of finishing touches on the overall look and functionality of your metal building. Details like doors, windows, paint finishes, and trim can enhance the appearance and usability of the structure.
Labor Costs Analysis
Selecting the right labor team is pivotal in accurately estimating the costs of constructing your metal building. When analyzing labor costs, it’s crucial to break down the expenses to understand where your money is being allocated. The cost breakdown should include wages, benefits, insurance, and any additional expenses related to the workforce. By having a detailed breakdown, you can identify areas where cost-saving measures can be implemented without compromising the quality of work.
Labor efficiency plays a vital role in determining the overall construction costs. Efficient labor practices can help in completing the project within the estimated budget and timeframe. Factors that contribute to labor efficiency include the experience of the workers, the use of advanced tools and equipment, and effective project management. By ensuring that your labor team is skilled and experienced, you can enhance productivity and reduce the likelihood of delays and cost overruns.
To accurately estimate labor costs, consider obtaining multiple quotes from different labor providers. This will give you a better understanding of the average market rates and help you negotiate a competitive price for the services required. Additionally, communicate openly with your chosen labor team to align expectations and ensure a smooth workflow throughout the construction process.
Factor in Permits
Factor in permits by thoroughly researching the specific requirements and associated costs before initiating the construction of your metal building. Permit application processes can vary significantly depending on your location and the size of the project. Contact your local building department to understand the necessary permits for erecting a metal building on your property. Be prepared for potential costs associated with permit applications, inspections, and adherence to construction regulations.
Before starting your metal building project, consider the types of permits you may need. Common permits include building permits, electrical permits, and plumbing permits. Each permit serves a specific purpose: to ensure your metal building meets safety and quality standards. Understanding and obtaining the required permits beforehand will prevent costly delays and fines during construction.
Construction regulations set by local authorities dictate how your metal building must be constructed to ensure compliance with safety and zoning requirements. Make sure to familiarize yourself with these regulations to avoid any violations that could halt your project. Additionally, factor in the time needed for permit approval when planning your construction timeline.
Account for Contingencies
When estimating metal building costs, it’s essential to account for contingencies to prepare for unexpected expenses during construction. Contingency planning is a vital aspect of budgeting for any project, ensuring you’re ready to address unforeseen circumstances without derailing your entire financial plan.
To effectively incorporate contingency planning into your cost estimation for a metal building project, it’s recommended to allocate a percentage of the total budget specifically for unexpected expenses. Typically, experts suggest setting aside around 5% to 10% of the overall project cost for contingencies.
This buffer can cover a range of unforeseen costs, such as material price fluctuations, design changes, or delays in construction due to weather or other external factors.
Review
As you navigate the intricate landscape of estimating metal building costs, remember that every penny counts.
Just as a skilled artist carefully selects each brushstroke to create a masterpiece, meticulous planning and attention to detail will ensure a successful and cost-effective project.
By following these tips and staying vigilant throughout the process, you can build a metal structure and a work of art that stands the test of time.
Recent Posts
What Are the Benefits of Tailored Metal Structures?
Imagine a well-crafted suit tailored to fit perfectly; that’s how tailored metal structures operate in
3 Tips for Long-lasting Metal Commercial Structures
When it comes to metal commercial structures, you’ll want to focus on a few key
Explore Benefits of Residential Metal Structures
It’s funny how you might stumble upon the idea of residential metal structures just when